Your Leading Environmental Engineering and Response Experts in the Upper Midwest
When you partner with Pinnacle Engineering, you gain access to a team of dedicated professionals who are passionate about environmental stewardship and finding practical solutions to complex problems. Our commitment to excellence, attention to detail, and focus on client satisfaction have established us as a trusted and reliable source for businesses’ environmental needs.
Navigating the complexities that come with environmental regulations can be overwhelming and costly. That’s why we specialize in providing comprehensive environmental services to help you tackle these issues head-on.
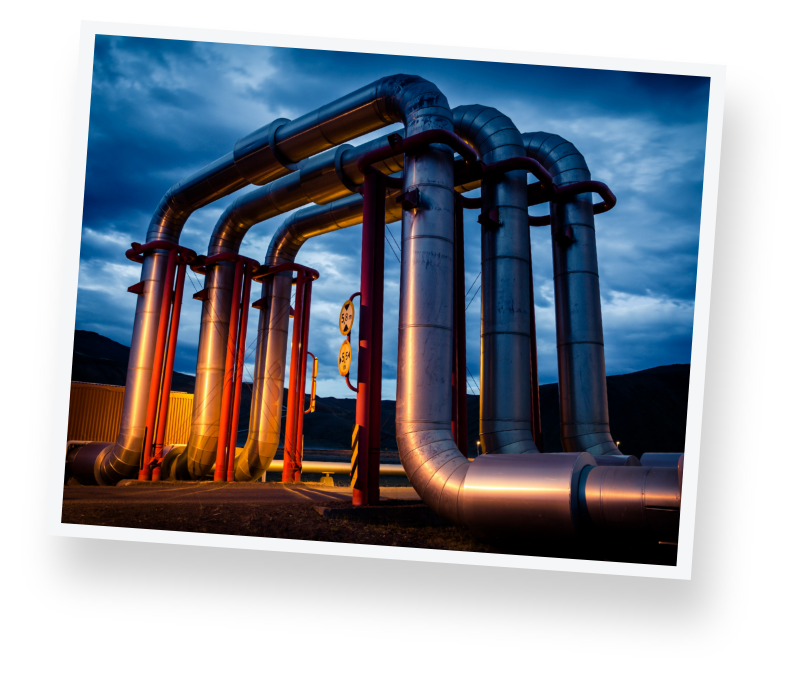
The midstream oil and gas industry is highly regulated at the local, state, and federal levels. Pinnacle Engineering’s oil and gas consulting services provide a regional presence to help you navigate regulatory compliance.
Pinnacle Engineering consults on greenfield site selection and offers full-service environmental permit support and engineering solutions to all markets.
Air permit compliance is highly complex due to the various federal and state regulatory requirements involved. As qualified consultants with over 30 years of environmental engineering experience, we understand the nuances involved in permitting and help ensure your facility is in compliance from day one.
Industrial manufacturing and renewable energy operations are required to submit reports for compliance with various state and federal regulations. With deadlines falling throughout the year, managing the creation and timely submission of reports on your own can be difficult.
At Pinnacle Engineering, we pride ourselves on being the pre-eminent choice for tackling our client’s environmental challenges head-on with urgency and efficiency.
Assisting clients in the rail industry by providing complete project solutions. We offer comprehensive assistance to railroad companies, covering all aspects of their day-to-day operations such as compliance, permitting, investigation, clean-up, and response.
Achieving, maintaining, and exceeding compliance with the myriad of environmental regulations. We have established ourselves as the ideal choice for clientele in effectively assessing, remediating, and maintaining potential risks and liabilities.
Navigating environmental complexities in the evolving landscape of energy operations. Our approach is characterized by in-depth expertise, unwavering dedication, and an integrated approach to environmental engineering.
Responding, monitoring, and resolving environmental emergencies from recognition to remediation. We understand the unique scope of work required for each response, and we strive to deliver timely and cost-effective, and efficient solutions for present and future risks.
Making informed decisions and managing potential environmental risks associated with a property. We help in achieving your environmental goals while ensuring the long-term value and sustainability of your assets.